We are committed to sharing unbiased reviews. Some of the links on our site are from our partners who compensate us. Read our editorial guidelines and advertising disclosure.
What Is In-Transit Inventory?
Any business that manages inventory knows what a headache it can be. Even with helpful inventory management softwares, it can be tricky to keep track of all the comings and goings—especially if some of your inventory hasn’t physically arrived yet.
In-transit inventory can be a great asset to your company, as long as it’s properly accounted for. Figuring out how much inventory you need to order, store, and budget for can be a little overwhelming, but with a few simple formulas and some great record-keeping, you’ll be able to master in-transit accounting. This skill will help you avoid problems like obsolete inventory and excess storage costs.
Let’s take a look at what defines in-transit inventory, who is liable for those items, and how to factor in the cost of waiting on a shipment.
What is in-transit inventory?
In-transit inventory (also called pipeline inventory) consists of any goods you’ve purchased that have not yet arrived. Depending on your line of business, goods are shipped from a manufacturer to either a physical store, a distribution center, or an ecommerce facility like a third-party logistics provider.
In-transit inventory ownership
When you purchase goods for your business, you will typically fill out a purchase order that includes the transfer of ownership. Typically, there are two types of in-transit inventory agreements.
FOB shipping point
Purchases listed as “free on board (FOB) shipping point” or “FOB origin” will transfer ownership to you (the buyer) as soon as they are shipped.
This is the more common type of inventory purchase because after shipment it places liability on you rather than the manufacturer.
FOB destination
The other type of inventory classification is “FOB destination,” in which ownership transfers to you when the items arrive. In this scenario, the seller owns (and is liable for) the in-transit goods until you receive them.
Inventory insurance
As most of your purchases will probably fall under FOB shipping point, it’s a good idea to take a look at your small business’s insurance plan and consider adding transit coverage. This coverage should be included under inventory coverage and will protect you from lost or damaged inventory.
By signing up I agree to the Terms of Use and Privacy Policy.
How to account for in-transit inventory
If the inventory you’ve purchased is classified as an FOB shipping point, you can list it as new inventory in your system as soon as it ships. For example, a used car dealership might list a preowned vehicle on its website as available for purchase even if it’s not physically on the lot yet.
If the inventory you’re waiting for is FOB destination, you won’t be able to account for it or offer it to buyers until it arrives at your service center.
Using an ecommerce inventory management software makes it easy to keep track of all your shipments and in-transit inventory.
Calculating in-transit inventory costs
Because businesses are typically liable for goods as soon as they’re shipped (FOB origin), they are technically paying for the storage of that in-transit inventory as well—even though it hasn’t physically arrived yet.
So, the first thing to do is figure out how much you typically pay to store inventory. This cost includes the maintenance of your storage facility (heating, rent, utilities), and any insurance you’ve purchased on your inventory. For a lot of businesses, storage will cost around 15% of the inventory purchase value.
For in-transit inventory, you’re paying for storage costs during the shipment waiting period, as well as once the items arrive. This means that the value of in-transit inventory depends on the number of days it takes to arrive after shipment.
The formula should look something like this:
Cost of inventory x Cost of storage / 365 = Daily value of in-transit inventory
Example
Let’s say you own a shoe company that orders $10,000 worth of new inventory, and shipments typically take two weeks to arrive in the United States. To calculate the cost of this in-transit inventory, try the following formula:
Cost of inventory ($10,000) x cost of storage (0.15)/ 365 = $4.10 per day of transit
Then multiply the daily value by your shipment waiting time.
$4.10 x Transit time (14 days) = $57.40
Once you have this calculation, the next time you order $10,000 worth of inventory, you’ll know to realistically budget for $10,057.40
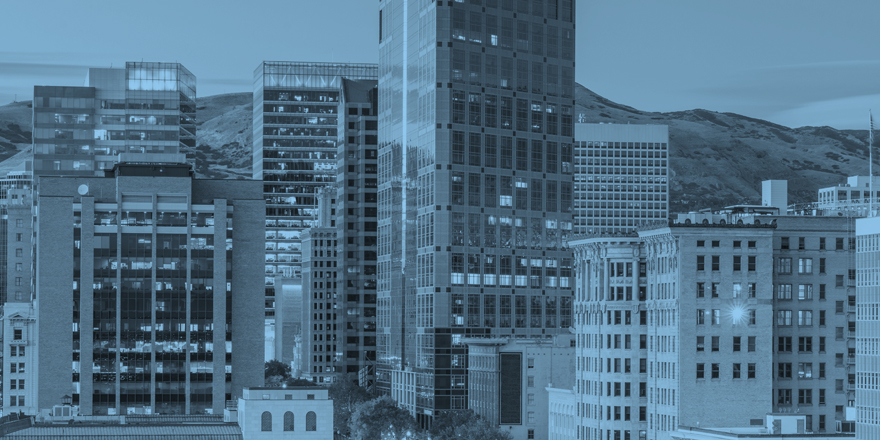
Ordoro offers everything you need to sell your products online or in person.
- Get total control over your inventory
- Align your business strategy with your stock management
- Maintain vendor and customer relationships
The takeaway
When managed and accounted for properly, in-transit inventory can be a great asset for small businesses. By having inventory on the way, your customers can order items that may have been out of stock otherwise. Just be sure to factor in the cost of transit items in your accounting and know whether or not they’re FOB origin or destination.
Want to learn more about inventory management? Check out The 14 Best Inventory Management Software for Small Businesses of 2022 on Business.org.
Related reading
In-transit inventory FAQ
As long as the in-transit inventory is classified as FOB shipping point or FOB origin, you should include those goods in your regular inventory.
Transit items are goods that the manufacturer has shipped but that have not yet arrived at your warehouse or storefront.
The cost of in-transit inventory is calculated by using the following formula: Cost of inventory x cost of storage / 365 x number of days in transit. This will help you determine the storage costs of inventory that you own but has not physically arrived yet.
For most businesses, you take ownership of the inventory as soon as it ships. This is called FOB shipping point or FOB origin, and it means you are liable for any lost items in transit. FOB destination signifies that the manufacturer retains ownership of items in transit.
Disclaimer
At Business.org, our research is meant to offer general product and service recommendations. We don't guarantee that our suggestions will work best for each individual or business, so consider your unique needs when choosing products and services.
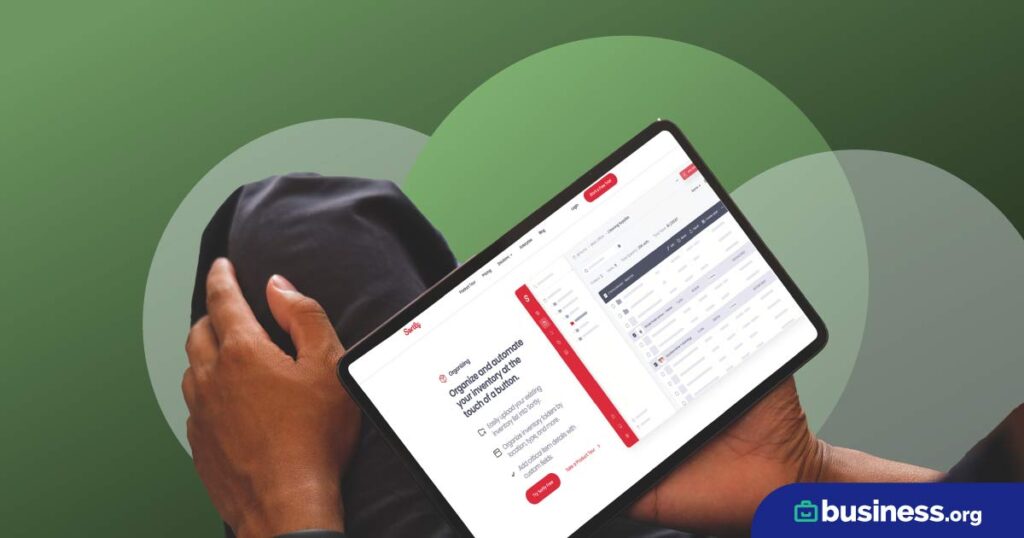
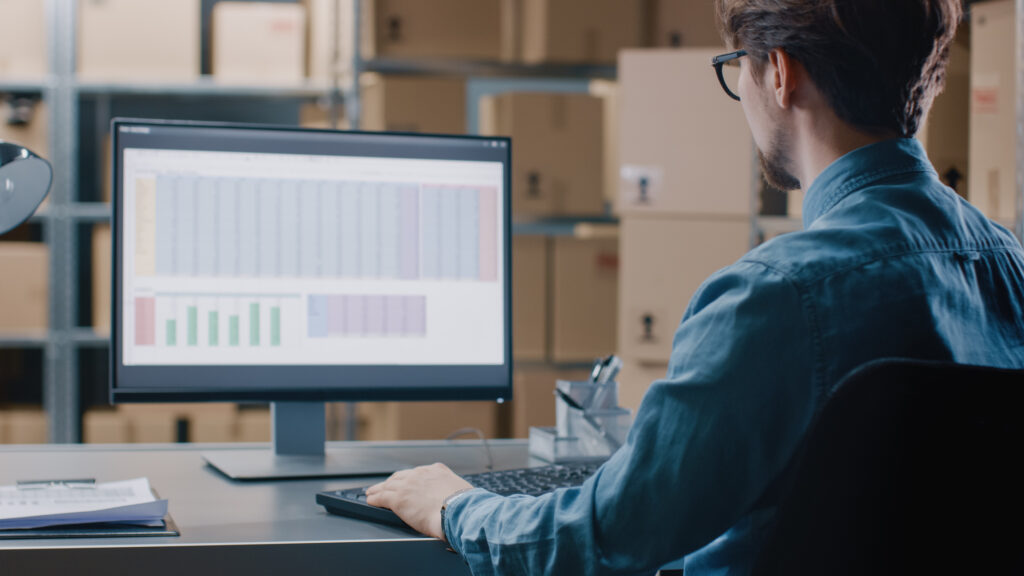
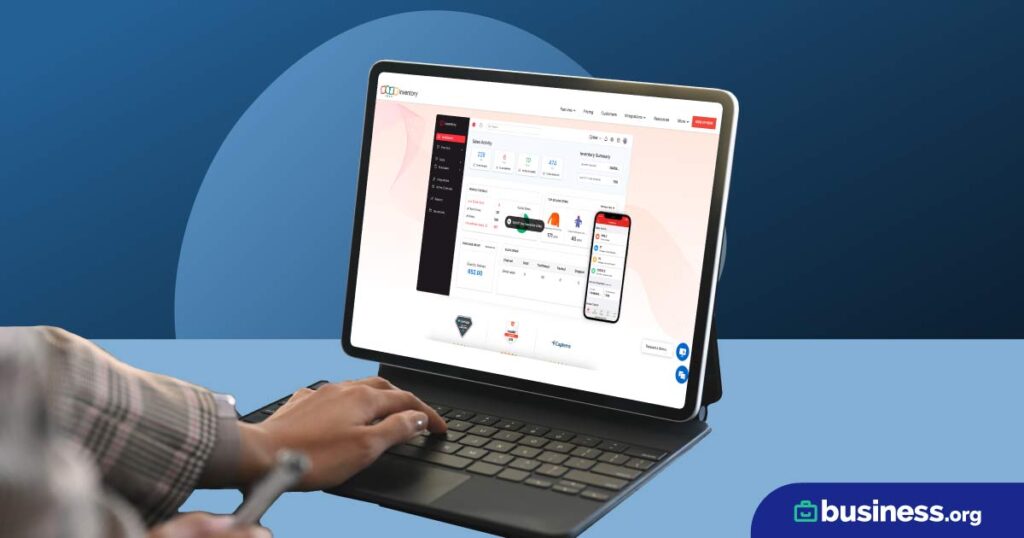
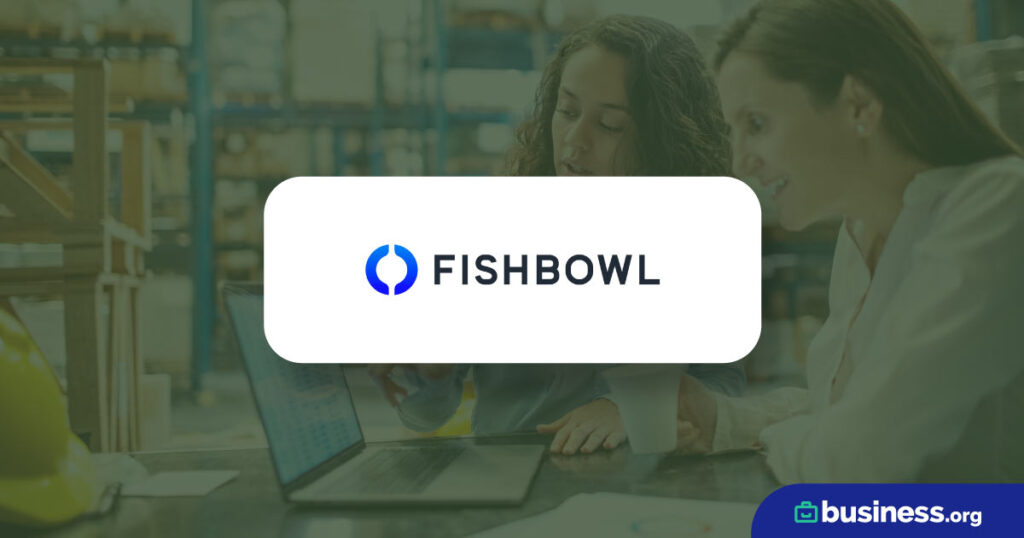