We are committed to sharing unbiased reviews. Some of the links on our site are from our partners who compensate us. Read our editorial guidelines and advertising disclosure.
Periodic vs. Perpetual Inventory Management
We reviewed and rewrote this article to make it more readable and accurate—thereby better helping you to suss out the difference between periodic and perpetual inventory systems and figure out the right method for your business.
The key difference between periodic and perpetual inventory management comes down to how often you take stock of your inventory levels. That may seem like an inconsequential decision, but it can have a significant impact on the accuracy and ease of your inventory tracking system.
Here’s everything you need to know about periodic and perpetual inventory management, how they affect your day-to-day business operations, and how they can impact your bottom line.
What is a periodic inventory management system?
When using a periodic inventory management system, you take physical counts of your inventory only periodically (hence the name). So if you take a physical count of your inventory at the end of each month, quarter, or year, this may be a good option for your business.
For many small businesses, this method makes a lot of sense. After all, if you maintain small inventory levels and stock a limited number of sellable products, it should take you only a couple of hours to tally the number of items on your shelves and calculate how many items you’ve sold.
The trouble with periodic systems, though, is that they don’t track inventory on an item-by-item or transaction-by-transaction basis. For starters, that makes it hard to identify accounting errors when they occur, and you can’t track product movement with as much accuracy as you could with a perpetual inventory system. But most importantly, periodic systems make it harder to accurately calculate your cost of goods sold (COGS).
To determine your business’s profitability, you’ll need to know how much you spent to produce, ship, store, and manage the inventory you’ve sold. The problem? Those costs can vary depending on the number of items you order at a time, the amount of inventory sitting in your warehouse, how tightly packed your shipping containers are, and the time spent processing new shipments.
Because periodic systems don’t track individual items and transactions, business owners have to calculate their cost of goods sold by adding the cost of their starting inventory to the cost of any additional inventory ordered, then subtracting the cost of their ending inventory at the end of the period:
Cost of goods sold = Beginning inventory + additional inventory - ending inventory
To determine the costs of your beginning, additional, and ending inventory, you have to keep careful track of purchasing and manufacturing costs for each order, the labor hours spent processing each batch of new inventory, and the amount of time each batch sits in storage. Then you’ve got to track which items actually get sold to determine the actual profit margins on each sale.
Sound complicated? That’s because it is. Granted, an inventory management software can automate a lot of those calculations, but there’s still a big margin of error—especially if your business stores a lot of inventory or offers more than a few product varieties.
By signing up I agree to the Terms of Use and Privacy Policy.
What is a perpetual inventory management system?
A perpetual inventory management system aims to track cost and stock levels on a transaction-by-transaction basis, perpetually updating costs associated with each item at every phase in the product life cycle.
Under a perpetual inventory system, individual items are given radiofrequency ID (RFID) tags, barcodes, or serial numbers to indicate their origin. This allows you to identify which purchase order the item came from (and the production and shipping costs per item on that order), how long the item has been on the shelf (and costs associated with storing that item for that time period), and even where it’s stored.
The result? When the item is sold, you can pinpoint exactly how much that specific item cost you. That makes your cost of goods sold more accurate, which makes your gross margin more accurate, which gives you (and investors, tax collectors, and lenders) a clearer picture of where your business stands.
With a perpetual inventory management system, you can pinpoint an exact cost of goods sold for each item you sell—getting a clearer picture of where your business stands.
There are a few drawbacks to a perpetual system, though. First, it can be a heavy lift for businesses trying to do their inventory tracking manually. So unless you have time to assign serial numbers to each and every item in your inventory by hand, then find and update the status for each item every time you make a sale, a perpetual system probably isn’t right for you.
Second, perpetual inventory systems are often more expensive than periodic systems. Like we said, it’s pretty much nuts to try to run a perpetual system by hand—meaning you’ll likely have to pay for an inventory management software. And if you opt to simplify the process further with RFID tags or barcodes, you’ll also need to invest in extra equipment (like scanners) and training to help your employees use your system correctly.
That said, we think inventory software and item-scanning equipment are well worth the cost. Between the two, you can automate most (if not all) of your inventory management, which saves you valuable time, reduces product waste, and gives you a more accurate idea of how much your business is spending and making.
The bottom line
In general, we recommend using a periodic inventory management system if you’re trying to track your inventory by hand. It requires less work for manual tracking, but it does make it harder to accurately allocate costs to the items you’ve sold. For that reason, we advise using a periodic system only if your business is small with low inventory levels, low product turnover, and a limited number of sellable products to track.
For all other businesses, we recommend using inventory management software to implement a perpetual inventory management system. This type of system is more accurate when it comes to cost allocation, and it automates a lot of the work that goes along with the inventory management process—especially when paired with an RFID- or barcode-scanning system.
Automation and individual item tracking are just a couple benefits of inventory management software. See what else inventory software can do for your business.
Disclaimer
At Business.org, our research is meant to offer general product and service recommendations. We don't guarantee that our suggestions will work best for each individual or business, so consider your unique needs when choosing products and services.
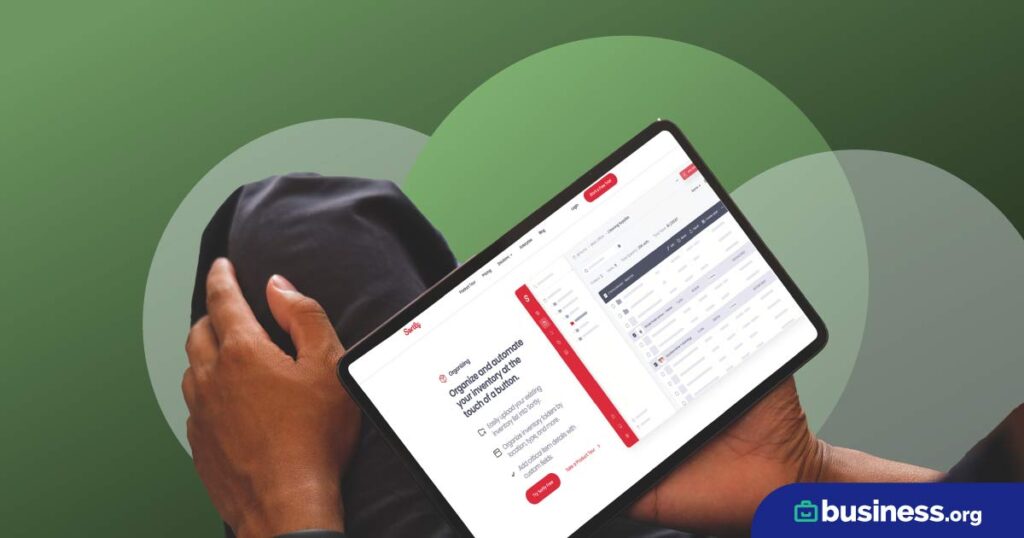
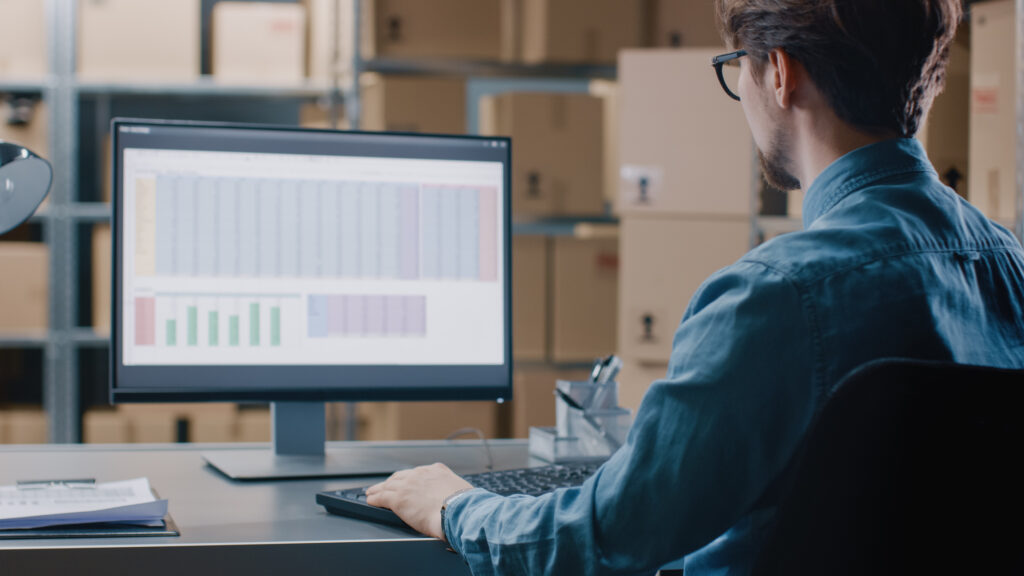
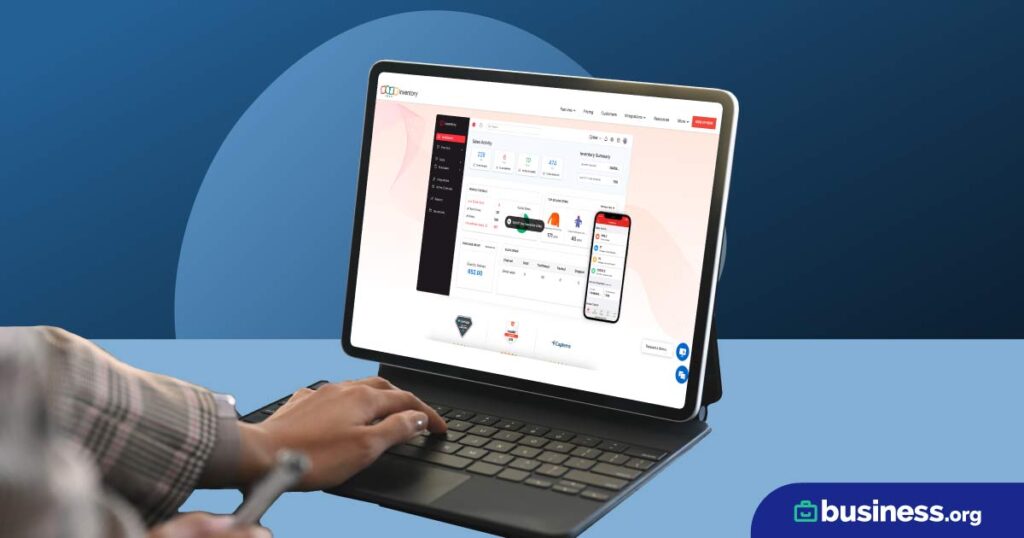
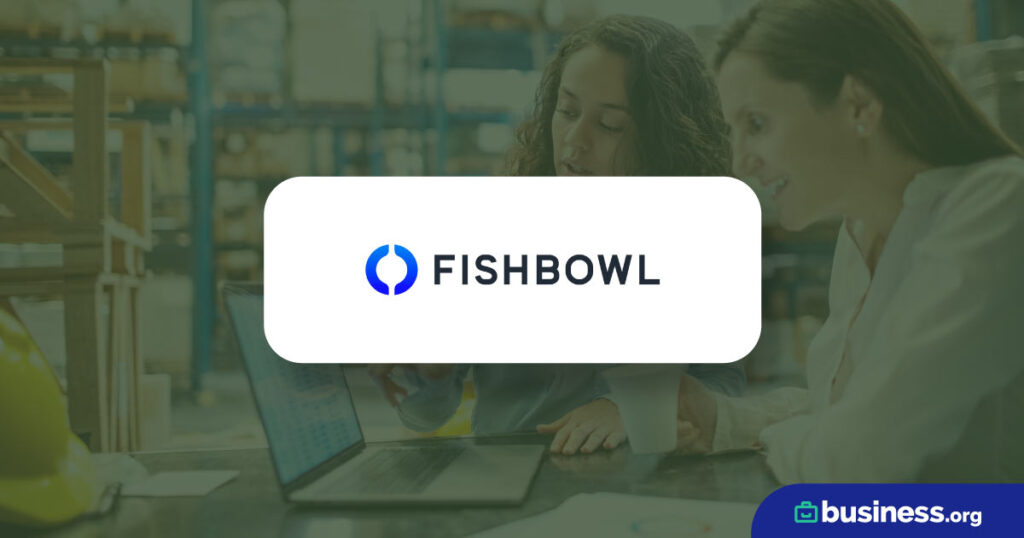