We are committed to sharing unbiased reviews. Some of the links on our site are from our partners who compensate us. Read our editorial guidelines and advertising disclosure.
Inventory Dos and Don’ts for COVID-19 and Other Supply Chain Crises
In early 2020, the coronavirus pandemic first began to pick up steam, stopping factories and business supply chains in their tracks. Since then, COVID-19 has continued to affect businesses around the globe—along with a fair number of other black swan events like the bushfires in Australia and the US.
While we certainly don’t expect every year henceforth to be a borderline apocalyptic series of disasters (à la 2020), the pandemic and other disasters this year have highlighted a need for most businesses to rethink their supply chain management.
So how do you prepare your business to withstand a supply chain crisis? We’ve broken it down into a list of dos and don’ts for increasing your supply chain resiliency going forward.
Dos and don’ts for supply chain resiliency
A black swan event is a totally unpredictable event that throws your supply chain way outside your normal parameters. Black swan events are very rare, but their consequences on your business may be severe. What’s more, preventative measures to black swan events often seem obvious in hindsight (“If we’d only done x, we would’ve been fine when y happened”).
DO: Prioritize products and goals
Let’s say a supply chain crisis like the coronavirus were to happen again, shutting down half your suppliers and logistics partners. How do you keep your business afloat when your supply chain is operating at half capacity?
That’s where it comes in handy to have a predetermined list of priorities ahead of time.
We recommend not trying to maintain all your inventory as usual. Instead, choose three to five items that generate the most profit or will be in the highest demand. Then devote all your remaining supply chain resources toward producing and shipping those items.
We also recommend identifying your business goals in advance, if possible. Is your number-one priority keeping the business afloat? Avoiding layoffs? Avoiding debt? Knowing these goals in advance helps keep you and your team on the same page on key decisions during a difficult time.
By signing up I agree to the Terms of Use and Privacy Policy.
DON’T: Put all your eggs in one basket
The first lesson of the coronavirus pandemic is to diversify your suppliers. If you rely on just one supplier for all your goods, you’ll be completely up a creek if anything ever happens to that supplier.
Along the same lines, it’s important to diversify the geographic area you rely on. Even if you’re using multiple suppliers, your production could come to a standstill if they’re all affected by a natural disaster in a single area. Partner with manufacturers in multiple areas of the world to protect your supply chain even further.
COVID-19 has also affected logistics and shipping, so we recommend you also diversify your logistics providers. That way, your business can still keep the supply chain running, even if your primary shipping provider goes under.
Finally, it’s extremely important to diversify your products and revenue streams. If you rely on sales of a certain product for the majority of your revenue, your business could easily lose everything if a supply chain crisis took away your ability to produce or ship that item. It’s important to find multiple high-profit items to fall back on. It’s also important to find alternative methods to make money—preferably methods that don’t rely on your supply chain at all (just in case).
DO: Plan for volatile customer demand
In times of crisis, customer demand can fluctuate wildly (and somewhat unpredictably). Look no further than the great toilet paper shortage of 2020 for proof of that.
If your company produces essential goods, you should make a plan to manage that customer demand as much as possible to reduce shortages.
A good example of this in 2020 was UK supermarket chain Tesco. To prevent stockouts on vital food supplies, Tesco launched an initiative to scale back production of certain food types and varieties. Instead, the company focused all its supply chain resources on staples like bread and milk. By doing this, Tesco largely managed to avoid shortages on key products—ensuring families throughout the UK were able to access vital supplies.
If your business doesn’t sell essential goods, make a plan that pinpoints demand triggers. For instance, a boxed hair dye company might see disruption to salon services as an indication that their product could be in high demand very soon. At that point, they might decide to ramp up their production in expectation of a demand spike—otherwise, they might keep production levels low to free up supply chain resources for essential goods and services.
DON’T: Create data silos
First, it’s important to make sure that all key decision makers within your organization have access to the complete picture when it comes to your supply chain. That means having an organized inventory system in place that everyone can access and knows how to use. If you can’t even identify where your inventory is, you can’t identify (and fix) breakdowns within your supply chain.
Increasing transparency also means developing closer relationships with your suppliers and logistics partners and sharing relevant data. Giving your third-party partners access to your sales and inventory data allows them to better anticipate your demand, which means a smoother, faster supply chain. And being able to gain insight into your manufacturers’ production capacity helps you make smarter decisions about when and how to reorder stock.
As part of this process, we also recommend learning as much as you can about your suppliers’ supply chains. Knowing where your manufacturer sources their raw materials and components gives you additional insight into your own supply chain.
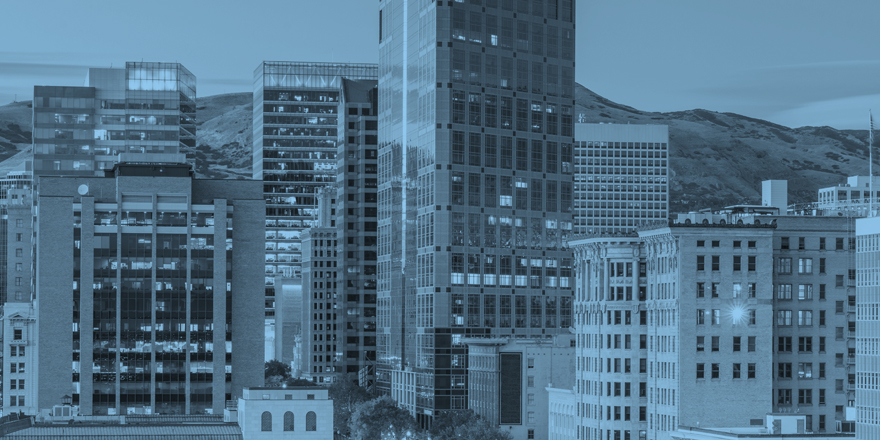
Ordoro offers everything you need to sell your products online or in person.
- Get total control over your inventory
- Align your business strategy with your stock management
- Maintain vendor and customer relationships
DO: Invest in technology
When the coronavirus hit, many businesses were thrown for a loop as they had to scramble to adapt their existing technology infrastructure to meet the new needs of remote workers. The biggest takeaway from this experience? Your business needs to invest in reliable technology before a major catastrophe makes it impossible for your employees to work.
If you operate a website or online service, invest in high-capacity servers that can keep up with increased traffic. If your business can operate with your employees working from home, scope out quality VoIP services that allow employees to make and receive business calls from their cell phones and laptops. Secure your computers with reliable firewall and VPN services to keep all your employees connected on a protected network, even when they’re working from many different locations.
Finding these solutions before a crisis hits gives your company the flexibility to adapt to any kind of new work environment so you can keep your business going longer.
DON’T: Assume it’ll never happen to you
Natural disasters, war, disease, terrorism—there are a lot of things that can seriously impact your business’s supply chain. Even relatively small things like trade wars, regulation changes, and labor disputes can affect your company’s ability to do business. That’s why you should have both short- and long-term contingency plans for any type of disruption.
These plans can include any of the following:
- Employee safety procedures. What’s the plan to keep your employees safe in the event of _____?
- Backup supply chain solutions. Who are your backup suppliers? Your backup logistics providers? What will you do if all shipping or transportation in a given area is shut down?
- Absenteeism workarounds. How will you accommodate having fewer employees or slower production times?
- Customer service response. How will you explain production slowdowns or shortages to your customers? What brand loyalty measures will you take to mitigate concerns?
- Succession plans. Who will take over if the crisis puts one or more members of your executive team out of commission?
Once you have these plans in place, make sure to educate your employees on how to implement those plans if needed.
FAQ about COVID-19 and supply chain crisis management
Is COVID-19 going away?
There’s a lot we don’t know about the coronavirus, but yes: eventually, the pandemic will pass. And with multiple vaccines already being administered, that time is coming soon. What might not go away so soon, though, is the impact that COVID-19 has had on businesses and their supply chains. And given the increasing instability in the world, it’s never a bad idea to improve your supply chain resiliency.
What should businesses do during the coronavirus pandemic?
Businesses’ number-one priority should be to keep their employees and customers safe. If possible, find ways to allow your employees to work from home. If your company can’t operate without in-person interaction, make sure to regularly disinfect surfaces and avoid having your employees share tools when possible. You should also make sure employees are able to social distance, and encourage your employees to wear masks while at work.
What can I do to cope with the effects of COVID-19 and quarantine on my business?
If your business has been affected by COVID-19, we recommend implementing some of our tips above to help stabilize your supply chain. Refocusing on your highest-value products and services can help you maximize your revenue while minimizing expenditures, which can help your business stay healthy in the midst of this crisis. If necessary, you can also seek outside business funding in the form of loans, grants, crowdfunding, and investors.
How long will it take to recover from COVID-19?
While most people recover from COVID-19 within two to six weeks, the economic impacts of the coronavirus will likely be felt for a lot longer than that. Unfortunately, we don’t have a magic 8 ball to tell us how long it will take for individual businesses to return to some semblance of normalcy. Nor can we predict how long it will take for the global economy to fully recover. All we know is we’ll likely continue to feel the ripple effects of COVID-19 for years to come.
The takeaway
COVID-19 has changed a lot about the business landscape—especially when it comes to inventory and supply chain planning. While the pandemic has thrown global supply chains out of sync for now, this black swan event has certainly illuminated some best practices for businesses going forward.
By following our list of dos and don’ts above, your company should be well on its way toward future-proofing your supply chain to withstand virtually any future crisis.
Looking to diversify your supply chain? Get started with our guide to finding and vetting new suppliers for your business.
Disclaimer
At Business.org, our research is meant to offer general product and service recommendations. We don't guarantee that our suggestions will work best for each individual or business, so consider your unique needs when choosing products and services.
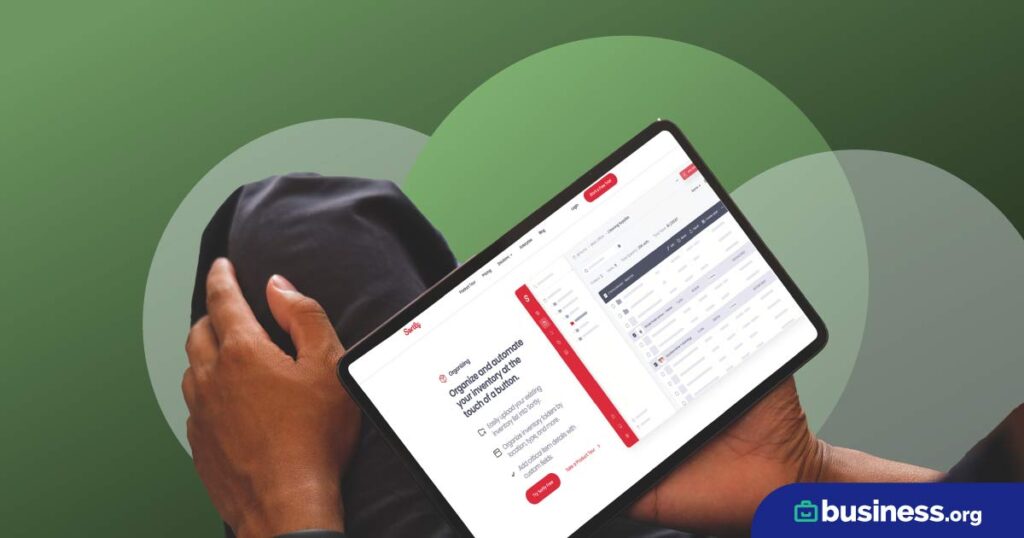
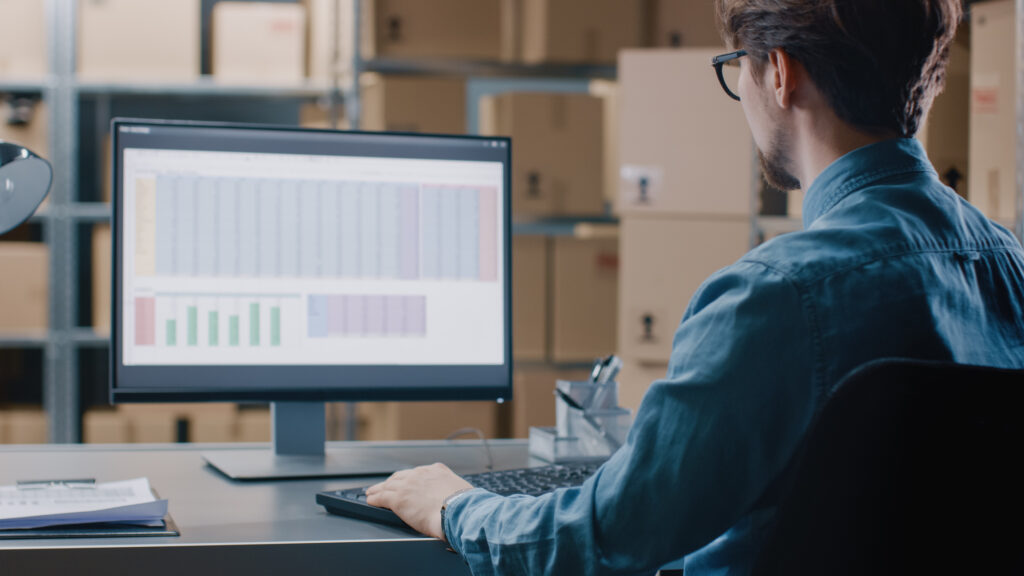
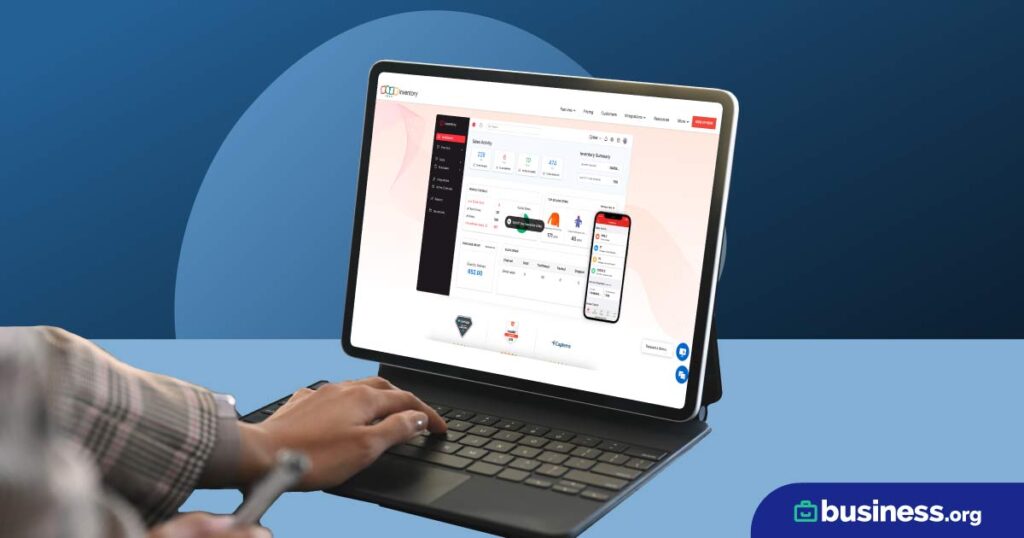
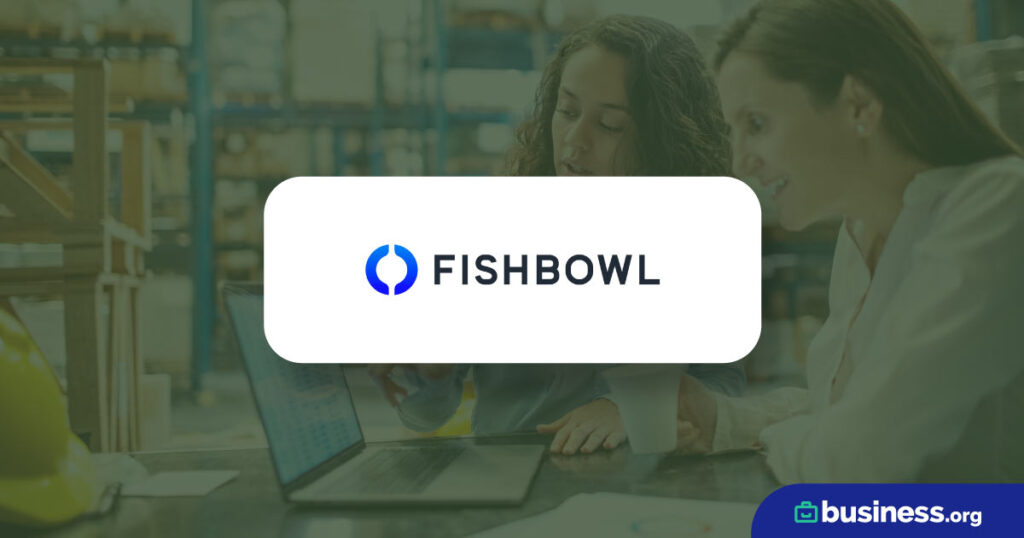